views
Introduction: Why Speed and Precision Matter in Aerospace
In today’s fast-paced aerospace industry, time is everything. Manufacturers must deliver high-quality products on tight schedules while maintaining strict safety and performance standards. Delays can lead to lost contracts, higher costs, and reputational damage. One of the key contributors to faster production without sacrificing quality is tooling engineering.
Tooling engineering refers to the design, development, and maintenance of the tools, moulds, and fixtures used during manufacturing. It plays a crucial role in transforming ideas into fully functioning aerospace systems. When paired with effective aerospace product development, tooling can significantly reduce development time and cost.
What Is Tooling Engineering?
Tooling engineering involves creating the hardware and support structures that allow manufacturing teams to build aircraft components accurately and efficiently. These tools guide machines and workers, ensuring repeatable processes that meet tight tolerances.
Key elements of tooling engineering:
-
Moulds and dies for shaping parts
-
Assembly jigs to hold components in place
-
Cutting, drilling, and forming tools
-
Inspection and test fixtures
Each tool must be engineered with precision, as aerospace parts must perform under extreme conditions—such as high temperatures, vibrations, and pressure changes.
How Tooling Engineering Supports Aerospace Product Development
Aerospace product development involves designing, testing, and producing parts and systems that meet specific flight or space mission requirements. Tooling engineering supports each stage of this process in the following ways:
1. Faster Prototyping with Custom Tooling
During early development, prototypes must be made quickly for testing. Tooling engineers design custom tools that help speed up this phase. This enables developers to test concepts, identify flaws, and make changes early.
Benefits:
-
Reduces time spent on revisions
-
Encourages rapid experimentation
-
Speeds up testing and certification
2. Improved Manufacturing Efficiency
Well-designed tools reduce the time it takes to manufacture each part. For example, automated jigs and fixtures position parts accurately for machining or assembly. This minimises human error and speeds up operations.
Features that improve efficiency:
-
Repeatable alignment systems
-
Tooling for automation and robotics
-
Quick-change setups for flexible production
3. Precision and Consistency in Production
Aerospace parts must meet very strict dimensional standards. Tooling ensures that every unit matches the original design exactly. This reduces waste, rework, and inspection failures.
How it helps:
-
Controls part tolerances tightly
-
Supports consistent material flow and shaping
-
Eliminates variations between units
4. Seamless Integration with CAD and Simulation
Modern tooling engineering uses 3D design software and simulation tools to create virtual models before any metal is cut. These tools integrate smoothly with product development platforms.
Advantages:
-
Validates tool performance before building
-
Detects design clashes early
-
Enhances collaboration between designers and engineers
5. Tooling for Composite Structures
As aircraft become lighter, composite materials like carbon fibre are replacing metal. These require specialised tooling such as autoclave moulds and resin transfer systems.
Impact:
-
Enables advanced material usage
-
Reduces structural weight without sacrificing strength
-
Improves aircraft fuel efficiency
6. Tool Maintenance and Lifecycle Management
Once tools are built, they must be maintained to keep production running smoothly. Tooling engineers track wear and tear, calibrate tools, and make updates when product changes occur.
Lifecycle activities:
-
Regular inspections
-
Predictive maintenance scheduling
-
Tool refurbishment or replacement planning
7. Compliance and Quality Assurance
The aerospace industry follows strict safety and quality regulations. Tooling engineering helps ensure every part meets the required standards by embedding quality checks into the process.
Examples:
-
Tooling includes built-in gauges and sensors
-
Fixtures are designed to allow easy inspection
-
Tool paths are validated for compliance
Real-World Example: Aerospace Fastener Production
Consider the manufacturing of titanium fasteners used in commercial aircraft. These components require exact threading, heat treatment, and finishing. Tooling engineers create custom dies and taps that produce thousands of identical fasteners quickly, safely, and with minimal waste.
This consistency is essential when fasteners are used in critical structural locations, where even a slight error could impact safety.
Future of Tooling Engineering in Aerospace
As the aerospace sector evolves, so does tooling engineering. New trends are shaping the way tools are developed and used:
-
Additive manufacturing (3D printing): Produces custom tooling faster than traditional machining
-
Digital twins: Create virtual models of tools to simulate wear and process efficiency
-
Smart tools: Include sensors that provide real-time data on temperature, pressure, or position
-
Modular tooling systems: Allow flexible use across multiple projects
These innovations help reduce development cycles even further, while supporting more complex aerospace designs.
Conclusion: Accelerating Innovation Through Engineering
Tooling engineering is more than just a support function. It’s a driving force behind efficient, precise, and scalable aerospace product development. From speeding up prototypes to enabling composite part production, smart tooling strategies save time and improve outcomes.
When done well, tooling engineering acts as the bridge between concept and reality. Aerospace companies that invest in modern tooling solutions are better equipped to innovate quickly, maintain high quality, and stay ahead in a competitive global market.
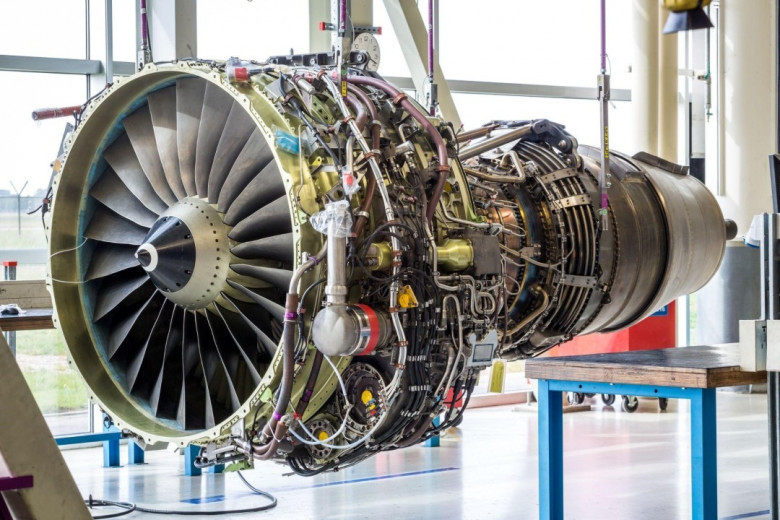
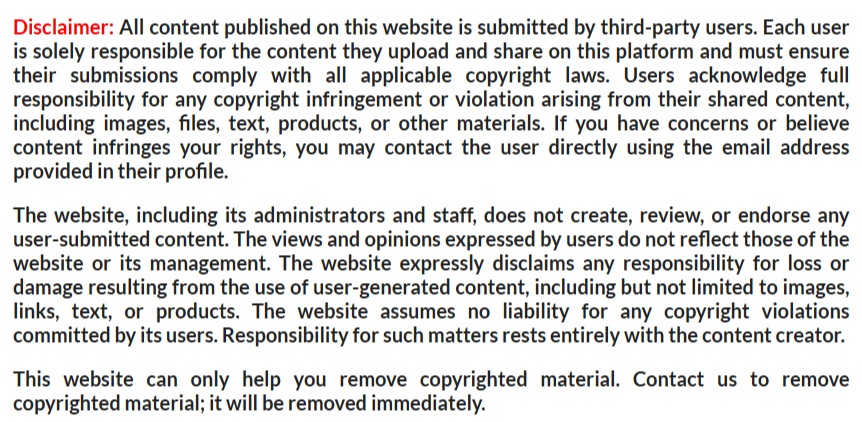
Comments
0 comment