views
At MyT Machining, we engineer high-precision components for industries that demand performance and durability—ranging from aerospace and medical to energy and robotics. Among the wide range of materials we work with, aluminum remains one of the most versatile and requested. Our expertise in aluminum machining enables us to deliver reliable results for clients needing strength, lightweight properties, and tight tolerances in both prototypes and full-scale production.
In this article, we break down the core concepts, materials, processes, and real-world applications behind aluminum machining, along with best practices for achieving consistent quality and performance.
Why Aluminum Is an Ideal Material for Machining
Aluminum offers a blend of properties that make it a top choice across industries:
● Lightweight and Durable
Aluminum is about one-third the weight of steel, yet certain alloys provide high strength-to-weight ratios suitable for structural parts.
● Corrosion Resistance
Thanks to its naturally forming oxide layer, aluminum is naturally resistant to rust and environmental degradation, especially when anodized.
● Excellent Machinability
Its relatively soft composition allows for faster machining, extended tool life, and superior surface finishes.
● Conductivity
Aluminum is both thermally and electrically conductive, making it ideal for electronic housings, heat sinks, and industrial enclosures.
● Recyclability
Aluminum is fully recyclable with no loss in properties, contributing to sustainability efforts in manufacturing.
These benefits make aluminum machining a valuable solution in product design, prototyping, and mass manufacturing.
Common Aluminum Alloys Used in Machining
Not all aluminum grades are the same. Different alloys offer varying strength, corrosion resistance, and machinability:
1. 6061-T6
The most commonly machined aluminum alloy due to its versatility. It offers good corrosion resistance, excellent strength, and high workability. Ideal for frames, enclosures, and structural parts.
2. 7075-T6
A high-strength alloy used in aerospace, motorsports, and defense. It’s slightly less corrosion-resistant than 6061 but offers superior strength.
3. 2024-T3
Known for fatigue resistance and high mechanical strength, though it has lower corrosion resistance. Suitable for aerospace fittings and fasteners.
4. 5052-H32
Offers high corrosion resistance, especially in marine environments. Commonly used in sheet metal applications and electronics enclosures.
5. MIC-6
A cast aluminum plate that is dimensionally stable and stress-relieved—great for tooling, jigs, and base plates.
Choosing the right aluminum alloy depends on the mechanical demands and environmental exposure of the part.
CNC Machining Processes for Aluminum
Aluminum can be machined using a range of CNC operations. Here’s a breakdown of the most common:
● CNC Milling
Aluminum’s softness allows high-speed milling for parts with complex geometries, pockets, and surfaces. Milling is ideal for face cutting, slotting, and 3D contours.
● CNC Turning
Used to produce cylindrical parts such as spacers, shafts, and bushings. Turning operations on aluminum are fast and highly repeatable.
● Drilling
With its excellent machinability, aluminum drills cleanly. Using sharp twist drills and lubrication reduces friction and improves hole accuracy.
● Tapping and Threading
Aluminum supports both internal and external threading. Proper tapping speeds and cutting fluids prevent thread galling.
● Surface Finishing
Machined aluminum takes well to a variety of finishes—anodizing, bead blasting, powder coating, or polishing—all of which can enhance function or appearance.
Surface Finishing Options for Aluminum Components
Post-processing is often required to improve wear resistance, corrosion protection, or visual appeal. Common aluminum finishes include:
● Anodizing
Adds a protective and decorative oxide layer. Available in clear or dyed colors. Improves corrosion and abrasion resistance.
● Bead Blasting
Provides a matte, uniform texture by removing surface irregularities.
● Powder Coating
Creates a durable, colorful finish with good environmental resistance.
● Chemical Film (Alodine)
Conductive and corrosion-resistant, useful in aerospace and electronics.
● Polishing
Used for consumer products where surface appearance is a priority.
Each finishing process must be chosen based on the intended use of the component and the alloy used.
Industries That Depend on Aluminum Machining
● Aerospace
Weight savings are crucial in aviation. Aircraft seat frames, structural supports, and interior components are often machined from 7075 or 2024 aluminum.
● Automotive
Engine components, transmission housings, wheels, and brackets rely on aluminum’s combination of strength and reduced mass.
● Medical Devices
Non-magnetic and corrosion-resistant, aluminum is perfect for surgical instruments and mobility equipment.
● Electronics
Enclosures, heat sinks, and internal frames for computers, tablets, and communication devices benefit from aluminum’s conductivity.
● Robotics and Automation
Aluminum components such as arms, brackets, and base plates are lightweight yet stiff, essential for high-precision motion.
Challenges in Aluminum Machining and How to Overcome Them
Even though aluminum is easier to machine than many metals, it presents specific challenges that must be managed:
● Built-Up Edge (BUE)
Aluminum tends to stick to cutting tools. Use sharp tools with coatings like ZrN or TiAlN to reduce friction.
● Chip Removal
Aluminum generates long, continuous chips. Chip breakers, air blast, or coolant help evacuate material and prevent clogging.
● Thermal Expansion
Aluminum expands more than steel under heat. Use stable fixturing and avoid excessive tool heat to maintain dimensional accuracy.
● Vibration and Chatter
Because of its softness, aluminum can amplify vibration. Using balanced tools, short overhangs, and stable feeds minimizes chatter.
Addressing these factors improves tool life, part quality, and machining efficiency.
Why Choose MyT Machining for Aluminum Components?
At MyT Machining, we don’t just cut aluminum—we engineer high-performance solutions tailored to your application. Here’s what sets us apart:
-
Advanced multi-axis CNC machines for complex geometries
-
Deep experience with aerospace, medical, and energy components
-
Expertise in selecting the right alloy and surface treatment
-
Quality assurance processes that include full inspection and documentation
-
Flexible support for both prototyping and full production runs
Whether you’re working on a custom part or a product line, we help you bring your aluminum design to life—accurately, reliably, and on time.
Have a project in mind? Let’s talk about how we can turn your concept into a precision-machined aluminum part built for real-world performance.
Conclusion
Aluminum machining remains one of the most valuable services in modern manufacturing due to aluminum’s unmatched versatility, strength-to-weight ratio, and ease of fabrication. From simple brackets to aerospace-grade components, CNC machining makes it possible to produce parts with complex geometry, tight tolerances, and professional-grade finishes.
The key to success lies in selecting the right alloy, optimizing machining parameters, and partnering with a machine shop that understands the unique challenges of working with aluminum. With the right expertise and tools, manufacturers can unlock aluminum’s full potential—creating components that are lightweight, durable, and ready for demanding applications.
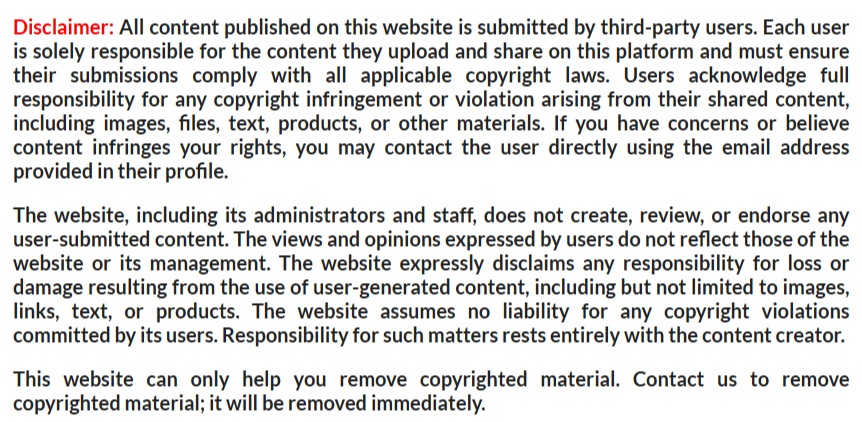
Comments
0 comment