views
Printed circuit boards or PCBs are the backbone of nearly all contemporary electronic devices. From your smartphone to your car's dashboard, PCBs offer the base on which electronics function. But ever considered how these complex boards are brought to life? The procedure may sound complicated, but when divided into stages, it's an intriguing blend of precision engineering and automation. Let's learn more about PCBs and PCB assembly in this write-up.
What Is a PCB?
A printed circuit board or PCB is a laminated board made from non-conductive materials (like fiberglass) and conductive layers (typically copper). Its primary role is to mechanically support and electrically connect electronic components.
A PCB’s layers usually include:
•Substrate (base layer): Provides structure and durability, often made of fiberglass or plastic resin.
•Copper layer: Conducts electricity and forms the circuit pathways.
•Solder mask: Covers the copper traces so that they do not come into contact with external elements. It also gives PCBs their distinctive green appearance.
•Silkscreen: Holds printed data, like component legends or labels, for debugging and assembly.
These components are placed over the PCB to build working circuits incorporated into electronic devices. But mere possession of a PCB is not enough—mounting these components onto it to build a workable board is where the wizardry begins.
The Process of PCB Assembly Explained
PCBA is where electronic components are mounted and soldered onto the PCB to make it functional. This complex procedure blends state-of-the-art machines with human expertise. Here is how it's done:
1. Step 1 – Application of Solder Paste
Solder paste is applied to the board in the first step of PCBA. Solder paste is a compound of small-sized metal solder particles and flux. Flux is responsible for holding the components on the PCB when it is soldered.
• A stencil is laid over the PCB to confine the solder paste to be applied only on certain areas, like the copper pads where the components will reside.
• Solder paste is applied over the stencil, creating precise deposits over the desired areas.
Consider this step as laying the groundwork for solid and consistent connections between the components and the board.
2. Step 2 – Component Placement
Then there is the automation-intensive process of putting electronic components on to the solder paste-covered PCB.
•Everything is carried out by Pick-and-Place Machines with such fast and precise speed. They utilize vacuum nozzles to pick components, position them, and set them on to their rightful places on the PCB.
•The machine is instructed through software that traces the PCB's layout so that components are put in place with accuracy.
This is the step that includes small items such as resistors and capacitors, and larger chips such as microcontrollers.
3. Step 3 – Soldering
After the components are placed in their correct locations, they must be fixed to the board forever. This is done by using one of two types of soldering techniques:
Surface Mount Soldering:
•Reflow Soldering: Reflow soldering is applied to surface-mounted components (SMDs). The PCB is processed in a reflow oven, where the solder paste is melted to form solid electrical and mechanical connections.
Through-Hole Soldering:
•For leads that need to pass through the board (through-hole components), wave soldering is applied. The PCB moves over a wave of molten solder that welds the leads to the board.
Every soldering process guarantees a strong bond without compromising the integrity of the components and the board itself.
4. Step 4 – Inspection and Quality Control
Quality control is paramount in any production process, and PCBA is not an exception. The board is thoroughly inspected to ensure that all the components are properly positioned, well soldered, and defect-free.
•Automated Optical Inspection (AOI): It employs high-definition cameras to scan the PCB automatically for alignment, missing parts, or solder faults.
•X-ray Inspection: For multilayer boards or high-density packaging, X-rays are employed to examine concealed solder joints and check internal connections.
•Manual Inspection: Highly skilled technicians can even conduct visual inspection, especially in the case of complex boards or low-volume productions.
5. Step 5 – Functional Testing
Following inspection, it's now time to check that the PCB functions properly. Functional testing is done by applying electrical signals and mimicking real-world working conditions to optimize performance.
•Circuit Continuity Testing: Verifies electrical paths are whole and operational.
•Performance Testing: Replicates the way the PCB will function inside its intended device to detect glitches or failure.
This is essential to ensure the final product fulfills design specifications and retains reliability.
6. Step 6 – Final Assembly
After passing all tests, the board is ready for use in the greater system. For instance, the finished PCB can be housed within a smartphone casing or integrated into an automobile navigation system.
At this stage, the PCB is finally cleaned to eliminate any remaining flux or impurities from the assembly process.
The Many Components of a PCBA Line
PCB assembly is so streamlined nowadays due to advanced machinery and technology. Some of the main equipment used are:
•Stencils: For applying solder paste.
•Pick-and-Place Machines: For placing components automatically.
•Reflow Ovens and Wave Soldering Machines: For accurate soldering.
•Inspection Machines: For quality checks.
These elements collaborate to guarantee that millions of electronic devices are constructed rapidly and uniformly.
Conclusion
PCB assembly is the behind-the-scenes hero of devices that make our daily lives possible. From the careful placement of solder paste to the exacting testing of the finished board, each process is guided by a combination of technology, innovation, and precision. The next time you swipe your phone screen, turn on your television, or turn on your computer, appreciate the labor that made it all possible.
Are you planning to use PCBA for your next project? A professionally populated PCB results in a stable, effective product. Contact industry specialists or reliable suppliers to have your designs realized accurately and with utmost care.
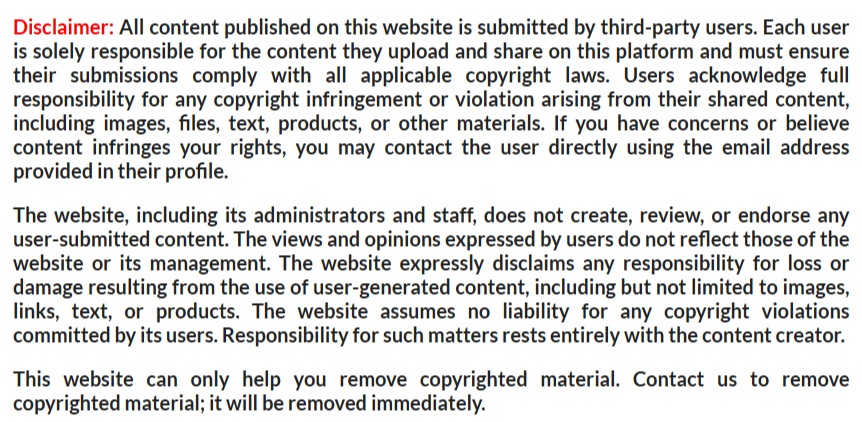
Comments
0 comment