views
The aerospace industry demands precision, durability, and reliability at an unmatched scale. Whether it’s a component in a commercial airliner or a part on a space-bound satellite, there is no room for error. That’s why CNC machining plays a central role in aerospace manufacturing. With its ability to produce high-precision parts repeatedly, CNC machining has become the backbone of aircraft component fabrication—especially when it comes to meeting the industry’s strict safety and quality standards.
Why CNC Machining Is Vital in Aerospace
Computer Numerical Control (CNC) machining enables the creation of complex parts with extreme accuracy, often within tolerances of ±0.0001 inches. In aerospace, even the slightest deviation from design specs can lead to catastrophic failure, making CNC the go-to solution for manufacturing critical components such as:
-
Turbine blades
-
Engine mounts
-
Aircraft structural supports
-
Avionics enclosures
-
Fuel system parts
-
Satellite components
Because these parts must endure high stress, extreme temperatures, and long lifespans, they require not just precision but also material consistency and surface integrity—features CNC machining readily provides.
Aerospace Safety Standards and Regulatory Compliance
To ensure safety and performance, aerospace components must adhere to rigorous industry standards. CNC machine shops serving the aerospace sector are expected to comply with:
🔹 AS9100 Certification
This is the gold standard for aerospace manufacturing quality systems. It encompasses ISO 9001 but adds requirements specific to aviation, space, and defense organizations.
🔹 NADCAP Accreditation
The National Aerospace and Defense Contractors Accreditation Program (NADCAP) focuses on special processes like heat treating, chemical processing, and non-destructive testing. CNC machining operations that integrate these processes must meet NADCAP standards to supply top-tier aerospace firms.
🔹 FAA and EASA Requirements
For parts used in flight, compliance with regulations from bodies such as the FAA (Federal Aviation Administration) or EASA (European Union Aviation Safety Agency) is mandatory. Each part must be traceable, verifiable, and fully documented.
These standards govern not only the manufacturing process but also material sourcing, part verification, and even packaging and shipping procedures.
Materials Used in Aerospace CNC Machining
Material selection is critical in aerospace CNC machining. These components must offer high strength-to-weight ratios, corrosion resistance, and performance under extreme conditions. Common aerospace materials include:
-
Titanium: High strength, low density, and excellent corrosion resistance
-
Aluminum Alloys: Lightweight and easy to machine, widely used in airframes
-
Inconel & Superalloys: Ideal for high-temperature environments such as jet engines
-
Stainless Steel: Used in fasteners and structural components
-
Engineering Plastics: For interior panels and lightweight covers
Each material requires precise cutting parameters and tool paths to ensure it meets the required tolerances and surface finish.
Role of Advanced CNC Machining Technologies
Modern aerospace CNC machining goes far beyond 3-axis milling. Advanced technologies now include:
-
5-Axis CNC Machining: Enables fabrication of complex geometries in a single setup
-
Live Tool Lathes: Combine turning and milling for streamlined workflows
-
Wire EDM & Sinker EDM: For intricate internal geometries and hard materials
-
Real-Time Monitoring Systems: Ensure that each cut stays within critical tolerances
-
CAD/CAM Integration: Allows engineers to simulate and optimize toolpaths before production
These tools ensure that aerospace parts are not only accurate but also consistent across production runs.
The Importance of Traceability and Quality Assurance
In aerospace, every component must be traceable back to its raw material batch and machining process. This is essential for safety audits, certifications, and in the rare event of part failure. Quality assurance procedures often include:
-
First Article Inspection (FAI)
-
Coordinate Measuring Machine (CMM) reports
-
Non-destructive testing (NDT)
-
Batch documentation and serial number tracking
Only machine shops with robust quality management systems are entrusted with these critical parts, underscoring the importance of experience and capability in the aerospace machining sector.
Choosing the Right CNC Machining Partner
To meet the aerospace industry's strict demands, it's essential to work with a provider that combines technical expertise, certified processes, and cutting-edge equipment. Reputable providers of cnc machining services deliver end-to-end support—from prototype development to full-scale production—while ensuring compliance with all relevant aerospace standards.
When evaluating a CNC partner for aerospace manufacturing, consider:
-
Certifications (AS9100, ISO 9001, NADCAP)
-
Industry experience and client portfolio
-
In-house inspection capabilities
-
Material sourcing and documentation process
-
Turnaround time and scalability
Working with a qualified CNC service provider reduces risk, accelerates product development, and ensures regulatory compliance from start to finish.
Final Thoughts
CNC machining has become indispensable to the aerospace industry due to its unmatched precision, repeatability, and ability to meet rigorous safety and quality standards. As aircraft designs become more advanced and materials more complex, the role of CNC will only grow in importance.
Whether you're manufacturing components for commercial aviation, space exploration, or defense systems, aligning with a certified and experienced CNC machining service is critical for success. Explore top-tier cnc machining services to ensure your aerospace projects meet the highest standards of performance and safety.
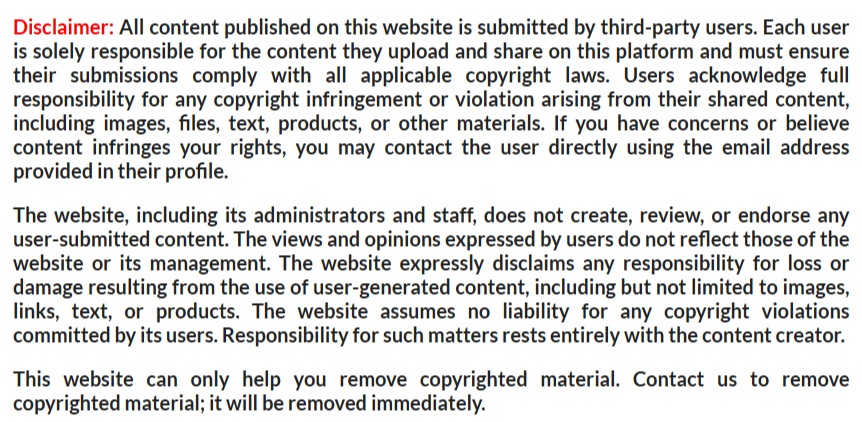
Comments
0 comment