views
Industrial environments demand systems that prioritize worker safety without compromising performance. In operations involving a material handling conveyor, safety considerations must begin at the design stage and extend through installation, training, and daily use.
A well-designed conveyor safeguards employees while sustaining operational flow, making worker protection an integral part of any material handling strategy.
Common Safety Hazards in Conveyor Operations
Operating a material handling conveyor introduces several hazards if safety is not addressed. Pinch points between moving parts, accidental entanglement, and falling materials remain common risks across many facilities. Inadequate guarding, improper start-up procedures, and manual jam-clearing increase the likelihood of injury.
Safety concerns grow exponentially when handling heavier loads or working in environments with limited visibility. Recognizing these hazards forms the foundation for creating safer industrial material handling environments.
Design Elements That Promote Safer Conveyors
Design decisions define how safe a material handling conveyor will perform in an active production setting. Key elements for injury prevention include fully enclosed moving parts, emergency stop mechanisms positioned within easy reach, and anti-slip platforms near operating areas. Incorporating soft starts and controlled stop mechanisms reduces sudden movements that can destabilize both loads and operators.
Custom guarding solutions built around industrial material handling conveyors help prevent unintended contact without restricting maintenance access. Belt tracking sensors, overload protection devices, and optical safety sensors provide real-time safeguards. These features reduce direct human interaction with moving conveyors and support hazard control through mechanical and electronic interventions.
Training and Operational Protocols for Safer Conveyor Use
Even the most securely designed material handling conveyor relies on human knowledge and behavior to maintain a safe workplace. Training programs guarantee operators, maintenance personnel, and supervisory staff understand operational risks and safe handling practices. Training covers proper start-up and shut-down procedures, lockout/tagout methods, emergency responses, and inspection routines. Reinforcing these practices through drills, refreshers, and visible signage around industrial material handling conveyors strengthens safe habits and minimizes accidents.
Supervision during operational shifts provides another layer of safety. Scheduled inspections identify potential mechanical faults early before each shift, reducing breakdown-related risks. A formalized safety reporting system encourages employees to report hazards without fear of reprisal, fostering an environment focused on continuous safety improvement.
Compliance with Conveyor Safety Standards
Adhering to standards such as ANSI B20.1 and applicable OSHA guidelines underpins responsible conveyor design and operation. Regulations dictate specifications for guarding, clearances, and emergency stops, among other requirements. Custom material handling conveyor solutions built with compliance in mind avoid common pitfalls and reduce the likelihood of citations or work stoppages.
Third-party audits and internal assessments of material handling conveyor operations strengthen compliance and reveal gaps requiring attention. Safe design and thorough documentation during the conveyor lifecycle demonstrate a company’s commitment to legal and ethical operating practices.
Contribution of Accumulation Conveyors to Safer Workplaces
Incorporating accumulation systems significantly contributes to workplace safety. An accumulation conveyor allows products to queue without requiring direct operator handling, minimizing risks associated with manual moving or stacking. Controlled product movement protects operators from sudden shifts or jams in conventional material movement setups.
Designed to buffer product flow at different stages of a production line, an accumulation conveyor reduces the need for manual intervention during product congestion. Less human interaction with live conveyor lines reduces pinch-point exposure and repetitive strain injuries, creating a safer, more predictable operating environment.
On a Final Note
Worker protection begins with intentional design choices, diligent training, and strict regulatory compliance in every material handling installation. Organizations that prioritize safety during conveyor selection and operation create healthier workplaces and build stronger operational resilience.
CONOVEY builds safer material handling and accumulation conveyor solutions to protect workers and production flow. Contact us now to safeguard every operation.
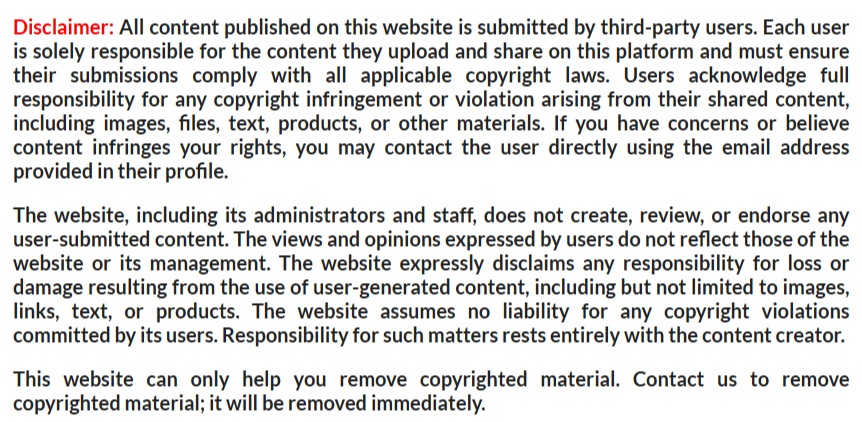
Comments
0 comment