views
Titanium has become a staple in modern medicine, revolutionizing everything from orthopedic implants to surgical instruments. Its unique combination of strength, biocompatibility, and corrosion resistance makes it one of the most sought-after materials in the healthcare sector. However, processing titanium into complex, patient-ready components is no simple task. It requires high-end engineering, experience, and innovation. At the heart of this transformation is medical titanium precision machining—a field dedicated to producing highly accurate, safe, and durable titanium parts for medical applications.
This article explores why titanium is ideal for healthcare, what makes its precision machining challenging and essential, and how today's machining solutions meet the rigorous standards demanded by the medical field.
Why Titanium is the Material of Choice in Medicine
Medical professionals and engineers alike favor titanium for several critical reasons:
-
Biocompatibility: Titanium is one of the few metals that is naturally accepted by the human body. It does not corrode in bodily fluids and doesn’t trigger allergic reactions.
-
Lightweight Strength: With a strength-to-weight ratio superior to most metals, titanium offers durability without bulk—a critical factor for implants and wearable devices.
-
Corrosion Resistance: Its natural oxide layer protects it from corrosion, ensuring that implants can last inside the human body for decades.
-
Fatigue Resistance: Titanium withstands repeated stress and strain, making it ideal for moving body parts like joints and prosthetics.
The increasing demand for custom implants, minimally invasive surgical tools, and long-lasting prosthetics makes titanium the clear choice for modern medical components.
The Role of Precision Machining in Medical Titanium Applications
Medical-grade titanium components must meet extreme standards for dimensional accuracy, surface finish, and cleanliness. This is where precision machining steps in. Using CNC (Computer Numerical Control) machines and advanced software, manufacturers transform raw titanium stock into detailed parts within microns of tolerance.
Precision machining is not just about shaping titanium—it’s about doing so repeatedly, reliably, and safely. Every deviation in a surgical tool or implant dimension can affect patient safety, device longevity, and surgical success. Precision ensures consistency.
Challenges in Medical Titanium Precision Machining
Although titanium is a high-performance metal, it poses distinct machining challenges that require advanced strategies and expertise.
1. Low Thermal Conductivity
Titanium retains heat at the cutting point, increasing the risk of tool wear, material warping, and poor surface finish. Without proper cooling and speeds, it can compromise both tool and material integrity.
2. High Strength and Hardness
Titanium's durability is excellent for the body but demanding on cutting tools. It requires specialized tooling and optimized parameters to maintain efficiency and finish quality.
3. Work Hardening
Titanium tends to harden during machining, especially if the cutting process is not continuous. Interrupted cuts or slow feeds can make the material even more difficult to machine.
4. Tight Tolerances
Medical applications require tolerances as fine as ±0.001 inches. This level of precision leaves no room for inconsistencies or surface imperfections.
Best Practices for Titanium Machining in the Medical Field
Meeting these challenges demands a combination of skilled craftsmanship, cutting-edge technology, and stringent quality control. Here's how leading manufacturers do it:
Use of Advanced CNC Machines
Multi-axis CNC milling and turning centers enable the production of complex geometries with a high degree of accuracy. These machines reduce the number of setups, minimizing the risk of errors.
High-Performance Tooling
Using carbide tools with proper coatings—like TiAlN (Titanium Aluminum Nitride)—increases heat resistance and tool life, resulting in better surface finishes and fewer tool changes.
Optimized Speeds and Feeds
Machinists carefully calculate spindle speed, feed rate, and depth of cut to maintain tool integrity and avoid workpiece damage.
Coolant Strategy
Flood coolant or Minimum Quantity Lubrication (MQL) systems help reduce heat buildup and maintain dimensional stability during cutting.
Cleanroom Machining and Deburring
Many medical parts are machined in cleanroom environments to prevent contamination. Deburring and finishing must also comply with medical hygiene standards.
Quality Assurance
Every part goes through rigorous inspections using CMM (Coordinate Measuring Machines), surface finish testers, and other metrology tools to ensure compliance with specifications.
Applications of Titanium Precision Machining in Healthcare
The range of titanium medical parts manufactured through precision machining is broad and continues to grow:
Orthopedic Implants
Titanium plates, screws, rods, and joint replacements for hips, knees, and spines require custom machining and exact fit for each patient.
Dental Implants
Machined titanium abutments and fixtures must offer high strength and biocompatibility while maintaining precise thread quality.
Cardiovascular Devices
Pacemaker cases and stents often incorporate titanium due to its non-reactivity and durability.
Surgical Tools
Forceps, scalpels, bone saws, and other surgical instruments must be not only sharp and ergonomic but also reusable and sterilizable without degrading.
Prosthetics
Titanium’s strength and light weight make it ideal for prosthetic joints and limbs, particularly in active users who demand both strength and comfort.
Meeting Medical and Regulatory Standards
Medical parts must comply with global standards to ensure they are safe, effective, and traceable. These include:
-
ISO 13485: Establishes a quality management system for medical device manufacturing.
-
FDA Compliance: Ensures that materials and processes meet U.S. Food and Drug Administration standards for safety and effectiveness.
-
ASTM F67 and F136: Define the specifications for unalloyed titanium and titanium alloys used in surgical implants.
-
Full Traceability: Every step, from raw material sourcing to final inspection, is documented for accountability and compliance.
Future Trends in Medical Titanium Machining
As healthcare becomes more personalized and technology-driven, titanium machining will continue evolving:
-
Micro-Machining: Miniaturized implants and devices require extremely small and intricate parts with micron-level precision.
-
Hybrid Manufacturing: Combining CNC machining with additive manufacturing allows faster prototyping and production of highly customized devices.
-
Smart Monitoring: AI-driven analytics and machine learning will improve quality control and reduce waste.
-
Sustainability: Eco-conscious machining practices and recycling of titanium chips are gaining attention in the medical supply chain.
Conclusion
Medical titanium precision machining is not just a manufacturing discipline—it’s a gateway to safer, stronger, and smarter healthcare devices. As titanium continues to dominate the medical materials market, precision machining ensures that each component meets the demanding expectations of surgeons, patients, and regulators alike.
From orthopedic implants to advanced surgical tools, the fusion of material science and machining innovation ensures titanium will remain a cornerstone of medical engineering for decades to come. Partnering with expert manufacturers who specialize in titanium machining is essential for delivering high-performance medical products that change lives.
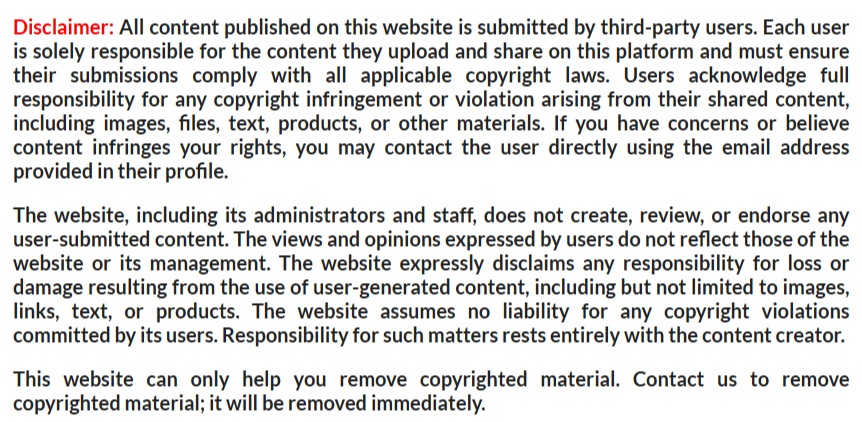
Comments
0 comment