views
In the world of precision electronics, the demand for exact electrical parameters has driven engineers to seek more refined methods of component calibration. One such method—laser trimming—has quietly revolutionized the accuracy and performance of resistors used in mission-critical applications.
A laser trim resistor is not just another passive component—it is a precision-calibrated element that plays a fundamental role in modern electronic systems, from aerospace instruments and automotive controls to high-end analog circuits and medical devices.
But what exactly is a laser trim resistor? How is it manufactured using a laser trimming machine? And what are the technical and performance advantages of resistors created by this method? This article explores these questions in depth.
1. What Is a Laser Trim Resistor?
A laser trim resistor is a resistor that has been finely adjusted or "trimmed" after production using a focused laser beam. The process allows for extremely precise calibration of the resistor's resistance value, often to within ±0.01% of the target.
Trimming is especially important in thick film or thin film resistor networks, where the initial printing or deposition process can produce small variations. A laser beam is used to selectively remove material from the resistive path, increasing resistance in a controlled manner.
This laser adjustment is permanent, stable, and does not degrade over time, making it ideal for circuits requiring exact voltage dividers, sensor conditioning, and current regulation.
2. How Does a Laser Trimming Machine Work?
The laser trimming machine is a highly specialized system designed to modify resistor values by precisely removing microscopic amounts of resistive material using a high-power laser beam. The machine typically includes:
-
Laser Source (often Nd:YAG or fiber laser)
-
Precision Motion Stage for X-Y positioning
-
Optical Microscope or Vision System
-
Real-Time Resistance Measurement Circuit
-
Computer-Controlled Feedback Loop
The trimming process generally follows these steps:
-
Initial Measurement: The system measures the initial resistance of the resistor.
-
Target Comparison: The desired resistance value is input into the software.
-
Material Removal: The laser ablates part of the resistive material—creating a groove or cut in the pattern.
-
Live Feedback Adjustment: As the resistance approaches the target, the system automatically slows down or halts trimming.
-
Final Validation: The trimmed resistor is re-measured to ensure accuracy.
The process is quick, non-contact, and can be applied to individual chips or entire resistor arrays on a substrate.
3. Types of Trimming Patterns
The way a resistor trimming laser removes material directly affects the resistor's thermal stability, noise, and power rating. Common laser trimming geometries include:
-
L-cut
-
U-cut
-
Serpentine trim
-
Notch trim
-
Step cut
These patterns are carefully selected based on the resistor’s application and the substrate material. For example, a U-cut offers greater precision for small adjustments, while a serpentine cut can create large resistance changes with low inductance impact.
4. Applications of Laser Trim Resistors
Laser-trimmed resistors are used where tolerance, temperature stability, and linearity are mission-critical. Applications include:
-
Medical Devices – Sensor amplification, ECG calibration
-
Automotive Electronics – Engine control units (ECU), ABS, airbag systems
-
Industrial Controls – High-precision motor drives and sensors
-
Test and Measurement Equipment – Oscilloscopes, voltmeters
-
Aerospace and Defense – Avionics, missile guidance systems
-
Audio and RF Circuits – Low-noise amplifiers, signal conditioning
These environments require components that behave consistently under harsh conditions. The resistor advantages offered by laser trimming—accuracy, stability, and low drift—are invaluable.
5. Advantages of Laser Trimmed Resistors
High Precision
Laser trimming can fine-tune resistors to within ±0.01% tolerance. This is unmatched by most traditional manufacturing processes.
Temperature Stability
Due to controlled trimming geometry and materials, trimmed resistors exhibit low TCR (temperature coefficient of resistance), ensuring accuracy over wide thermal ranges.
Low Noise
The precise trimming process minimizes structural damage to the resistive film, resulting in low voltage and current noise—ideal for sensitive analog applications.
Permanent Adjustment
Once a resistor is laser-trimmed, the change is permanent, and no aging or drifting occurs under normal operating conditions.
Non-Destructive
Since the trimming is contactless and does not disturb the underlying substrate, the electrical and mechanical properties of the circuit are preserved.
6. Comparison With Other Trimming Methods
Before lasers, resistor trimming was done using methods like:
-
Mechanical scribing
-
Sandblasting
-
Chemical etching
Compared to these, resistor trimming lasers offer:
-
Better resolution and control
-
Fewer defects or thermal damage
-
Capability to trim in real-time with automated feedback
-
Smaller feature sizes and better pattern fidelity
Laser trimming is now the gold standard for precision resistor manufacturing.
7. Integration With Modern Electronics Manufacturing
Laser trimming isn’t just a lab-scale process. Modern laser trimming machines are fully automated, computer-controlled systems that can be integrated directly into SMT (Surface Mount Technology) lines. They can work with:
-
Single resistors
-
Resistor networks or arrays
-
Hybrid microcircuits
-
Substrate-level trimming before packaging
This allows for in-line calibration, reducing post-production testing and rework. Manufacturers using this process experience improved yield, better component performance, and shorter product development cycles.
8. The Future of Laser Trimming Technology
With the rise of IoT, EVs, aerospace miniaturization, and smart sensors, the demand for laser trim resistors is only growing. Innovations in trimming lasers now include:
-
UV laser trimming for even higher precision and smaller heat zones
-
AI-driven control systems that adjust cut patterns dynamically
-
Machine vision integration for automated component alignment
-
Multi-layer trimming on stacked or 3D substrates
As circuit complexity increases, so will the importance of this "invisible" technology that powers precision behind the scenes.
Conclusion
So, what is a laser trim resistor? It’s far more than a resistor—it’s a precision-calibrated device crafted through advanced laser engineering. Whether used in life-saving medical equipment or space-grade avionics, the laser trimming machine ensures that every resistor performs exactly as intended.
With the resistor advantages of high accuracy, stability, and durability, laser trimming has become an indispensable part of modern electronics manufacturing. And with ongoing advancements in resistor trimming laser technologies, we are just scratching the surface of its full potential.
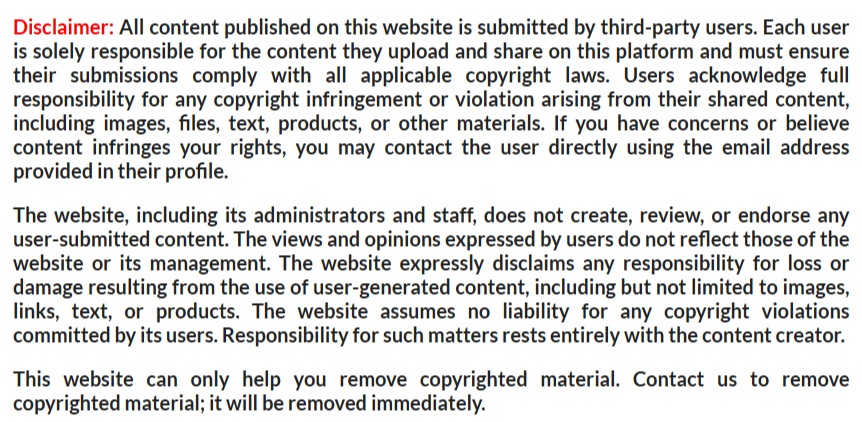
Comments
0 comment