views
Designing printed circuit boards (PCBs) has become more than just a technical process—it’s a strategic task critical to electronics innovation. In today's competitive landscape, industries from consumer electronics to aerospace demand high-speed, compact, and reliable PCBs. This is where efficient layout planning makes a real difference. By leveraging tools and techniques that support smarter layout practices, PCB layout services are now more crucial than ever.
Among the many software platforms available, OrCAD X has gained attention for its modern, scalable design flow and robust planning features. Though tools matter, design methodology, layout flow, and adherence to industry best practices contribute equally to creating an optimized PCB layout.
Why Optimizing PCB Layout is Essential
An optimized PCB layout doesn't just reduce size, it ensures signal integrity, enhances thermal performance, simplifies testing, and reduces time to market. Whether you're working on a compact wearable device or a multi-layered control board for automotive systems, layout precision determines success.
Poor layout planning leads to EMI issues, high return rates, and costly iterations. As a result, many organizations are now outsourcing or enhancing their PCB layout services to reduce risks and improve performance during the early design stage.
Key Principles of Effective PCB Layout
Before delving into specific techniques, let’s outline the foundational principles for any successful PCB layout:
1. Component Placement Strategy
Start with a logical flow of components. Group components based on function, keep high-speed components close to connectors, and avoid placing sensitive analog components near noisy digital ones.
2. Signal Path Optimization
Trace routing should follow the shortest and most direct path. Reduce via usage where possible and always route differential pairs symmetrically to maintain signal integrity.
3. Power Integrity and Grounding
Using a dedicated ground plane helps minimize EMI. Place decoupling capacitors near power pins, and ensure current return paths are short and low impedance.
4. Thermal Management
With higher current densities in compact layouts, efficient heat dissipation becomes essential. Use thermal vias, heat sinks, and copper pours to manage hotspots.
Adopting Layer Stack Planning Techniques
The number and type of layers directly influence board performance. For example, a 4-layer board with a dedicated ground and power plane ensures better EMI shielding and return path control.
Proper stack-up planning can also assist in impedance matching for high-speed signals. Signal layers should ideally be adjacent to ground planes, maintaining tight coupling and minimizing cross-talk.
Design Rule Checks (DRCs) and Constraint Management
DRCs are vital to identify spacing violations, unconnected nets, and improper routing. Advanced constraint management allows design teams to set specific rules for:
Trace width and clearance
Differential pair spacing
Impedance control
Length matching
Automation in this area saves valuable time and prevents downstream issues during prototyping and manufacturing.
Advanced Techniques for Optimizing PCB Layout
Let’s explore the hands-on techniques and strategies to elevate PCB layout efficiency:
1. Blind and Buried Vias
For compact designs, blind and buried vias enable higher component density while maintaining signal flow and mechanical integrity.
2. Teardrop Pads
Used at trace-to-via junctions to enhance structural stability and prevent stress fractures in high-vibration environments.
3. Length Tuning for High-Speed Signals
Timing mismatches in high-speed signals can lead to data errors. Length tuning and serpentine routing help match delays across signal pairs, especially in DDR or USB routing.
4. Via Stitching for Ground Shielding
Stitching vias along the edges of ground planes ensures EMI containment and promotes better return path continuity.
Role of Simulation in Layout Planning
Pre-layout and post-layout simulations such as signal integrity (SI), power integrity (PI), and thermal simulations have now become standard in high-performance designs. These simulations predict layout-related issues early and guide design adjustments before manufacturing begins.
By embedding simulation into the layout process, PCB layout services reduce design rework, improve compliance, and help create more reliable electronics.
Leveraging Modern Tools for Layout Efficiency
Today’s EDA tools offer AI-assisted suggestions, cloud collaboration, and real-time feedback. This is particularly relevant when using advanced platforms like OrCAD X, which enhances the designer’s ability to visualize, simulate, and optimize layouts within a unified interface.
Incorporating features like layer stack management, real-time DRCs, and 3D visualization, OrCAD X transforms conventional layout planning into a more intuitive and error-proof process. A comprehensive breakdown of these features and techniques is outlined in this in-depth resource on PCB layout planning with OrCAD X, providing practical guidance for professionals aiming to streamline their design process.
Common Challenges in PCB Layout and How to Overcome Them
Despite having powerful tools and services at hand, layout challenges still persist. These include:
1. Limited Board Space
Solution: Use high-density interconnects (HDI), multi-layer stack-ups, and component miniaturization.
2. Signal Reflection and Interference
Solution: Employ proper termination, controlled impedance traces, and maintain separation between analog and digital signals.
3. Thermal Issues
Solution: Perform thermal simulations, use thermal vias, copper pours, and spread heat-generating components strategically.
4. Library Management Errors
Solution: Centralize component libraries and ensure each symbol and footprint is validated for pin mapping and dimensions.
Collaborative Layout Planning
In modern electronics development, collaboration across teams of hardware engineers, layout designers, mechanical engineers, and software teams is essential. Modern layout platforms support version control, real-time feedback, and collaborative review systems.
Cloud-based platforms and shared project environments also allow PCB layout services to coordinate remotely, reducing delays and miscommunications.
Post-Layout Validation Best Practices
Once the layout is complete, validation ensures the design is ready for prototyping and fabrication. Key validation tasks include:
Gerber and drill file generation
Design for manufacturability (DFM) checks
3D mechanical verification
Bill of Materials (BOM) cross-verification
Running post-layout checks in accordance with industry standards (IPC, RoHS, etc.) ensures the board will function as expected and meet regulatory compliance.
The Future of PCB Layout Optimization
As electronics become more compact, faster, and multifunctional, layout planning will demand even more precision. We can expect increased use of AI in routing, predictive error checking, and real-time cloud simulation.
In response, PCB layout services are also evolving. Designers now need to combine creative thinking with robust technical knowledge and tool expertise.
Future layouts will not only require meeting functional goals but also sustainability objectives, such as reduced material waste, recyclability, and energy-efficient manufacturing processes.
Conclusion
Optimizing PCB layout is not a one-time task—it’s a continuous improvement process that merges intelligent design, tool proficiency, and technical foresight. From component placement to simulation, every step matters in achieving high-performing and reliable electronic products.
Using modern tools like OrCAD X, supported by streamlined methodologies and professional PCB layout services, engineers can minimize design cycles, reduce cost, and improve product performance. And for those diving deeper into tool-specific strategies, exploring guides such as How to Use OrCAD X for PCB Layout Planning can significantly enhance your layout efficiency.
By staying aligned with the latest layout trends and best practices, engineers and teams can build the electronics of tomorrow with confidence and precision.
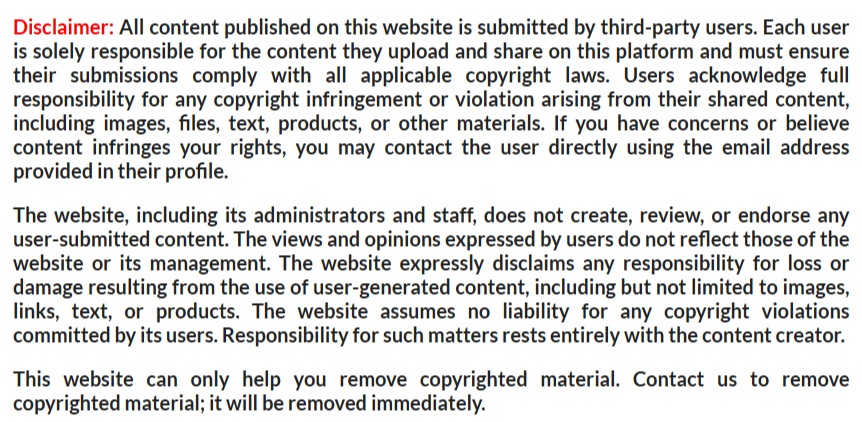
Comments
0 comment