views
Prototype Injection Molding has become an essential tool for product developers seeking efficient, cost-effective, and precise methods of turning innovative concepts into tangible parts. This manufacturing process allows for the rapid production of prototype parts using injection molding techniques, providing engineers and designers with the opportunity to test and refine their products before full-scale manufacturing. In this comprehensive guide, we will explore the ins and outs of Prototype Injection Molding, its benefits, applications, material considerations, and how to select the right partner for your development projects.
Understanding the Basics of Prototype Injection Molding
Prototype Injection Molding is a process in which plastic materials are injected into a mold cavity to produce prototype parts that closely resemble the final product. This technique bridges the gap between initial design concepts and mass production, offering a way to validate functionality, aesthetics, and manufacturability. Unlike traditional injection molding used for large production runs, Prototype Injection Molding focuses on creating a small batch of parts—often in quantities ranging from a few units to a few hundred. This allows developers to identify design flaws, make iterative improvements, and shorten the overall product development timeline.
For product developers, understanding how Prototype Injection Molding works is critical to maximizing its advantages. The process starts with designing a mold, typically made from aluminum or softer steels, which can be fabricated quickly and at a lower cost compared to hardened steel production molds. Molten plastic is injected into these molds under pressure, solidifies, and is ejected as a finished part. The precision and repeatability of Prototype Injection Molding enable developers to test various design iterations under realistic conditions, ensuring that their product is ready for mass manufacturing with minimal risk of costly design changes later on.
Key Advantages of Prototype Injection Molding for Product Development
One of the main reasons Prototype Injection Molding is so popular among product developers is the speed it offers. Traditional tooling for full-scale production can take months to design, machine, and validate, whereas prototype molds can often be created in just a few weeks or even days. This rapid turnaround allows developers to bring new products to market faster, which is especially critical in competitive industries like consumer electronics, automotive, and medical devices. Speed doesn’t come at the expense of quality either—Prototype Injection Molding delivers high-precision parts that meet tight tolerances and can undergo rigorous testing.
Another advantage is cost-effectiveness, particularly during the early stages of product development. Producing low-volume parts through Prototype Injection Molding is significantly cheaper than investing in production-grade tooling right away. The use of less expensive materials for molds and the ability to produce only the quantity needed for testing helps companies conserve resources. Moreover, Prototype Injection Molding supports design flexibility, allowing for multiple iterations and modifications without incurring excessive costs. This iterative process leads to better product designs and reduces the likelihood of costly changes during mass production.
Material Selection and Design Considerations in Prototype Injection Molding
Choosing the right material for Prototype Injection Molding is crucial to the success of the prototype and, ultimately, the final product. A wide variety of thermoplastics can be used, including ABS, polycarbonate, polypropylene, nylon, and more. The selection depends on the intended use of the prototype part, such as mechanical strength, heat resistance, or chemical stability. Developers may also opt for materials that closely mimic the properties of the final production material to ensure that testing accurately reflects real-world performance. Collaborating with material suppliers or Prototype Injection Molding partners can help identify the most suitable resin for each application.
Designing for Prototype Injection Molding requires attention to moldability, part geometry, and function. Developers must consider factors like wall thickness, draft angles, and undercuts, all of which affect mold construction and part ejection. Simplifying the part design can reduce tooling complexity and costs while speeding up production. It’s also important to anticipate potential challenges such as warping or sink marks, which can occur with certain materials or part designs. Working closely with experienced mold designers during the prototype stage ensures that the part can be produced efficiently and will function as intended during testing.
Applications and Industries Benefiting from Prototype Injection Molding
Prototype Injection Molding is widely used across various industries due to its ability to produce functional parts that meet strict performance standards. In the automotive sector, it plays a key role in developing components like housings, connectors, and interior parts, where precision and durability must be validated before committing to mass production. Consumer electronics companies rely on Prototype Injection Molding to create enclosures, buttons, and structural parts that can be tested for ergonomics, fit, and aesthetics. The ability to rapidly produce parts that resemble final production pieces allows for faster refinement and certification processes.
The medical device industry is another area where Prototype Injection Molding has significant impact. Medical components, such as surgical instruments, diagnostic device housings, and implantable device parts, must meet stringent regulatory standards. Prototype Injection Molding allows developers to create functional prototypes that can be tested for biocompatibility, sterilization compatibility, and mechanical performance. Similarly, in the aerospace and defense sectors, Prototype Injection Molding supports the development of lightweight, high-strength parts that can undergo rigorous environmental and mechanical testing. Its versatility makes it an indispensable tool for product developers in nearly any field.
How to Choose the Right Prototype Injection Molding Partner
Selecting the right Prototype Injection Molding partner is essential for achieving a successful outcome in product development. Developers should look for a provider with a proven track record in delivering high-quality prototype parts within tight timelines. Experience in working with a wide range of industries and materials is another important factor, as it ensures the partner can offer valuable insights on material selection, design optimization, and manufacturing challenges. A good partner will also provide comprehensive support throughout the development process, from initial design reviews to final part validation.
Additionally, it’s vital to assess the technological capabilities and services offered by the Prototype Injection Molding provider. Look for partners who utilize advanced mold-making technologies, such as CNC machining and EDM, as well as robust quality control processes to ensure part consistency and accuracy. Some providers may also offer value-added services, such as secondary operations (e.g., painting, assembly) and engineering support, which can streamline development. Building a strong relationship with a reliable Prototype Injection Molding partner not only accelerates time-to-market but also reduces risks and ensures that the final product meets or exceeds expectations.
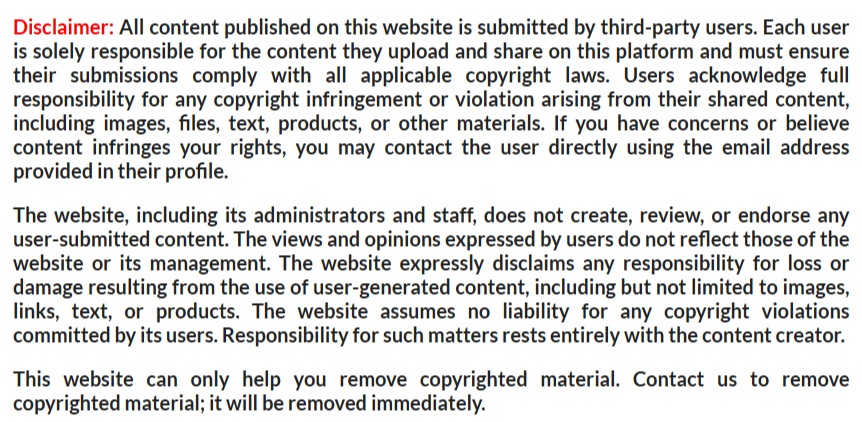
Comments
0 comment